Visit our Quality Solution Page to learn more about QualityOne.
“IF YOU CAN'T DESCRIBE WHAT YOU ARE DOING AS A PROCESS, YOU DON'T KNOW WHAT YOU'RE DOING.”
-W. Edwards Deming
Unraveling the Process Approach
At its core, the process approach demands that you identify your organization's processes, their inputs and desired outputs, and how these processes interconnect and influence one another.
From approving suppliers to shipping products and gathering customer feedback, quality and manufacturing professionals are immersed in processes daily. Essentially, every action within your organization can be defined as a process. As one of ISO's seven quality management principles, the process approach ensures organizations deliberately plan processes and their interactions to achieve objectives. It's vital to understand process interactions and dependencies since the output of one quality management process often becomes the input for another.
The Significance of the Process Approach
ISO 9001:2015 further accentuates the process approach, highlighting its importance. Let me share an anecdote to illustrate this point: At a previous company, I experienced chaos after the implementation of a new customer feedback/call center system. The complaints department became overwhelmed by non-complaint customer issues due to inadequate planning of process interactions. With proper planning, this issue could have been avoided altogether.
Implementing the Process Approach with PDCA Cycle
The PDCA (Plan-Do-Check-Act) cycle simplifies the process approach by integrating processes and their interactions with risk-based thinking at every step. Additionally, it inherently supports the continual improvement of your quality management system.
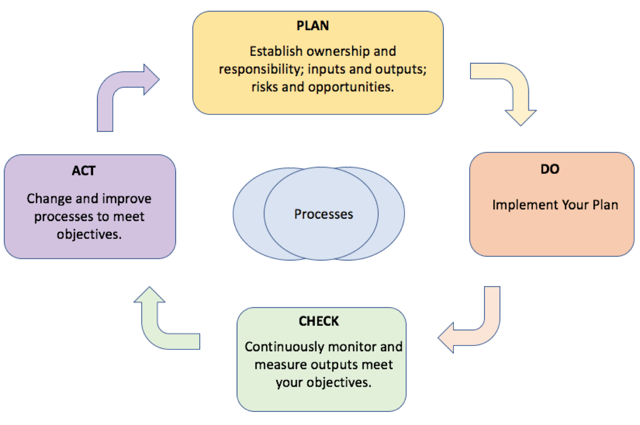
Discover the Right Tools for Determining Process Inputs and Output
Process maps are an excellent way to visualize individual processes and their interactions, ultimately helping you meet ISO 9001:2015 requirements. There are various tools available depending on your objective and the complexity of the process. Here are three of my favorites:
- SIPOC Diagram: Offers a high-level view of the process by outlining the supplier, input, process, output, and customer. This diagram provides an overview of internal and external process impacts and can be complemented with detailed flowcharts for complex processes.
- Turtle Diagram: Delivers a more detailed view of a process, defining associated documentation, supporting processes, owners, equipment, and evaluation criteria for meeting objectives.
- Swim Lane Flowcharts: Detailed process maps that indicate specific actions and ownership, perfect for situations involving multiple departments or participants.
Defining your processes and their interactions is crucial for organizations to operate effectively and efficiently. It enhances understanding of ownership and responsibilities, considers risks and opportunities, and establishes a process that supports continual improvement of your quality management system, ultimately helping you meet ISO 9001:2015 requirements.
In our final post of this series, we will explore ISO 9001:2015 expectations for leadership responsibilities and performance evaluation of the QMS.
Wishing you a quality-filled day!
Want to align your ISO 9001:2015 practices with a top-notch quality management solution? Discover Veeva's QualityOne on our product page.
SHARE